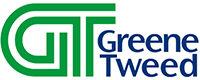
Job Information
Greene Tweed Engineer II -Quality in Kulpsville, Pennsylvania
At Greene, Tweed, you'll find the cutting-edge technology, world-class polymer expertise and endless advancement opportunities you'd expect from a multi-national industry leader. You'll find them all in an environment that embraces diversity in people and opinions, moves decision making to the point of impact, and celebrates your success.
If you enjoy continuous learning and are excited about working with and creating technological solutions, explore career opportunities with Greene, Tweed.
Assist Quality Engineering Supervisor as liaison between Manufacturing Value Streams, Quality and Engineering relative to customer specifications, customer quality requirements, and customer problems.
Facilitate all APQP activities, assess and mitigate the risk for the company.
Lead all PPAP activities related to Process Flow Maps, DFMEA, PFMEAs, Control Plans, Gage R&R studies, Capability Studies, Statistical Process Control, & 100% Inspection reduced to a Sampling Plan via Capability Analysis with cross-functional team members.
Lead continuous improvement and new product development of manufacturing processes using Six Sigma methodologies.
Perform design of experiments and create processes for reacting to statistical process control as required to facilitate process improvement.
Manage customer complaints and analysis of claims for assigned value stream. Perform root cause analysis with a cross functional team and make recommendations for corrective action.
Provide coaching and mentoring to the value stream on 8D problem solving methodology and facilitate root cause analysis and corrective action activities.
Provide Quality support to incremental & new product developments as assigned. Responsible for facilitating development and implementing Quality Plans and Manufacturing Process Control Document.
Work closely with GT Supply Chain and Value Engineering team on supplier related quality issues and provide technical expertise on product specifications.
Understand the incoming critical specifications required to maintain final Product Quality. Work closely with customers, gathering the Voice of Customer on Quality requirements where applicable.
Review technical documents from Customers and interpret them from a Quality perspective to support applications engineering with quality capability in DFM process.
Write necessary controlled documents such as but not limited to quality procedures, work instructions and forms as required. Mentor and coach Quality and Value Stream members on advanced statistical tools and analysis.
Note: This Job Description in no way states or implies that these are the only duties to be performed by the employee occupying this position. Employees will be required to follow any other job-related instructions and to perform any other job-related duties requested by the Supervisor. All requirements are subject to change and updates.
Minimum 3 years experience with quality engineering responsibilities in a manufacturing industry. Facilitated all APQP activities such as PFM's, FMEA's, Controls Plans, Gage R&R, FAI's, Values Stream Mapping.
Have experience with 8D Problem Solving Methodology along with knowledge of 5 Why's, Fishbone Diagrams, FTA, 7 Basic Quality Tools and continuous improvement initiatives (DOE).
Analyze historical and real-time data to understand process and equipment trends, characteristics, dependencies on other upstream processes.
Collaborate cross-functionally at various levels from manufacturing technicians to senior managers across the organization in solving problems.
Demonstrated proficiency in applying Six Sigma methodologies to reduce manufacturing variability and of Lean methodologies to reduce and eliminate waste.
Must have demonstrated a record of achievement in problem solving.
Experience leading and developing continuous improvement projects.
Have exceptional analytical&critical thinking and be action oriented.
Working knowledge of ANSI Standards for engineering drawings and Geometric Dimensioning and Tolerancing.
Knowledge of elastomers and thermoplastics preferred.
The referenced salary range is based on the Company's good faith belief at the time of posting and any applicable collective bargaining agreements. Actual compensation may vary based on factors such as geographic location, work experience, market conditions, education/training and skill level.
We also provide eligible employees with a competitive benefits package that includes health insurance, flexible spending accounts, health savings account, 401k savings plan, life and disability insurance, tuition assistance and more, to meet the diverse needs of all employees and their family members.
Equal Opportunity Employer:
Greene, Tweed is an Equal Opportunity Employer. Employment decisions are made without regard to race, color, religion, gender, sexual orientation, gender identity, national origin, age, physical or mental disability, veteran status, or any other federally protected class.
Drug Free Workplace:
Greene, Tweed is a Drug Free Workplace. Employment is contingent upon successful completion of a pre-employment drug screening and background investigation subject to federal, state, and local laws.
NOTE: Greene, Tweed is not seeking assistance or accepting unsolicited resumes from search firms for employment opportunities, unless they have a written agreement for the position they are contacting us about. Regardless of past practice, all resumes submitted by search firms to any employee at GT without a valid written search agreement in place for that position will be deemed the sole property of Greene, Tweed, and no fee will be paid in the event the candidate is hired by Greene, Tweed as a result of the referral or through other means.
Where Inspiration Drives Innovation
At Greene Tweed we believe that our true capability as a technology-focused company comes from our employees. Every customer challenge is solved by a team, and members are engaged across departments. From engineering and manufacturing, to sales and marketing, we work together using cutting-edge technology to assess problems, recommend solutions, and bring them into reality.
The tools of social business bring voices from around the world together in collaboration. And advanced capabilities such as FEA and state-of-the-art laboratories allow for comprehensive testing, analysis, and predictive modeling. Our manufacturing facilities expand the limits of possibility in fabrication. And embedded Lean Six Sigma upholds the highest levels of quality and efficiency during production.
This process of development is fundamental to Greene Tweed’s ability to solve critical challenges. And it means going beyond the right tools, and seeking out the right people.